Inside a multimillion dollar airplane spare part factory
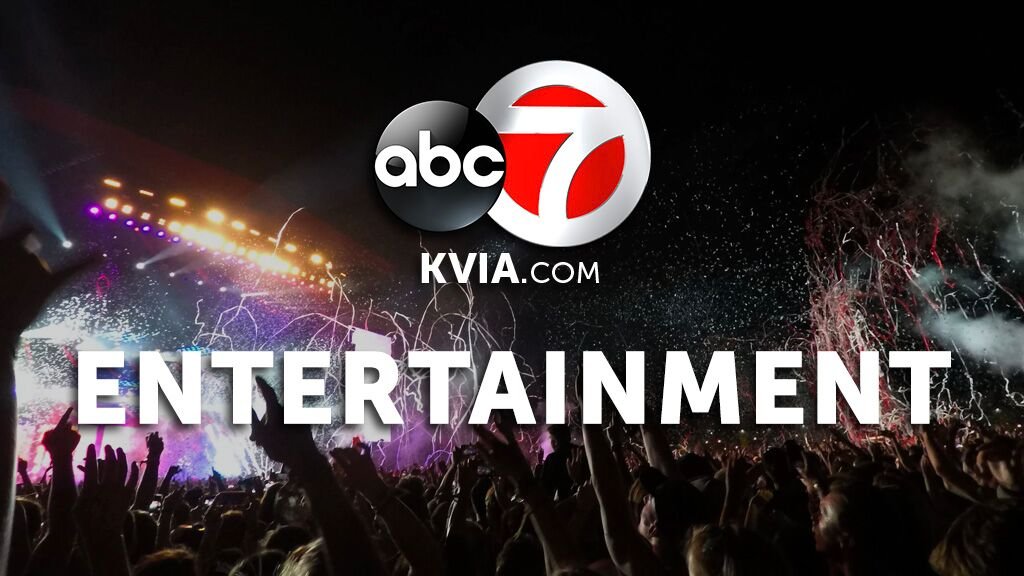
We’ve all been there: you board your flight and get settled in, only to find out there’s an issue with the airplane and you’ve got to wait until the new part arrives before you can jet off.
Eventually, the airplane’s ready to go, albeit about an hour later than planned.
But what went on behind the scenes while you were clock-watching and waiting for take off?
AJW Group is an aviation company responsible for supplying spare parts to some 6,000 aircraft across the world, servicing operators from budget airline EasyJet to business jet manufacturer Bombardier.
CNN Travel was given a recent tour of AJW’s UK headquarters to see what it’s like inside an airplane spare part factory.
Once a small operation run out of a modest warehouse near Gatwick Airport, south of London, AJW is now a multimillion dollar business, with thousands of spare parts ready to spring into action.
It receives 155,000 import and export orders a year — and the CEO has a helicopter on the roof.
Behind the scenes
Inside AJW’s sprawling UK headquarters, situated just outside the unassuming English village of Slinfold, is a giant warehouse housing everything you’ll ever need on an airplane.
Literally, everything — from toilet cleaner to airplane seats and seatbelts, tires — and, soberingly, airplane flight recorders, the “black boxes” that are used by investigators to determine the cause of air crashes.
In an adjacent glass office building, president and CEO Christopher Whiteside, an aviation expert who took over AJW 15 years ago, explains how the company operates.
“We own and manage the assets primarily, really any spares — from a seal or a filament to an engine — and we move that stuff around,” he tells CNN Travel.
“We hold it in dedicated warehouses, or we move it around the global network and we also repair that material.”
Whiteside uses an example — imagine there’s an A320 at Gatwick with a reported technical problem. Airplanes can fly in various states of disrepair, but if the technical fault has deemed the aircraft not airworthy, something has to be done ASAP.
The first step is the pilot identifying the problem and communicating the issue with the on-ground team.
It might be the airline has a spare on hand and the engineer can fit it, in which case the issue is resolved on site.
“If they don’t have one, they’ll call one up from somebody like us,” says Whiteside.
“We have literally millions of spare parts and, and hundreds of millions of dollars worth of value in this material — located everywhere from Buenos Aires to Birmingham to Hong Kong.”
Airlines will be keen to get the problem solved quick. It’s not just an inconvenience for customers, an AOG sitting unmoving could cost the airline thousands of dollars an hour.
“The numbers are enormous,” says Whiteside.
Over in the warehouse, Andy Smith, group operations director, demonstrates how this works in real time.
“We receive about 1,000 shipments a day,” says Smith, who, back when he joined AJW in 1986, was the company’s eighth employee.
“So it could be anything from something we purchased, something that we sent out for repair that’s coming back, it could be something that is coming in for repair.”
Arrivals are unloaded by courier in a secure area, then logged by AJW workers and put into stock. If it’s a used item that needs repairing, it’ll be fixed — quickly if stock levels are low, later if there’s no urgent demand.
The exception to that rule is the extensive work that AJW does for EasyJet. The European budget airline owns all its own stock, so it’s not up to AJW to decide whether or not it goes out for repair.
Each part, no matter how big or small, arrives with an airworthiness certificate and other paperwork. It gets taken apart and reassembled in the workshop, with every move taken carefully documented.
An internal system keeps track of everything from purchasing, repair, management, accounting, and stock control.
This database also lets Smith and his team know the status of the aircraft awaiting the spare part.
“It could be to Gatwick, it could be to Russia,” says Smith. “[The system] will give us a time remaining clock on the right hand side — but an AOG from the point of order from the customer to ready for shipment, the KPI is 45 minutes — it has to be out here as quickly as possible.
It’s busy all year round, says Smith. In the summer, it’s all about keeping EasyJet airplanes in the air. In the winter, they’re doing all the off-season maintenance.
“I would say there is always about 200 fix slips on there constantly,” he says, gesturing at the computer screens in the warehouse. “24 hours, 365 days a year. It just doesn’t stop.”
Due diligence
AJW’s workers handle dangerous goods regularly, and have the appropriate training. They also have to consider a part’s provenance, and where it might be going next.
“If someone buys a part from you, you have to do your due diligence about where and what they’re doing with that part. You can’t just give it to them and go, ‘Well, it’s not my problem,'” explains Smith.
The company always asks for aircraft registration, he says.
Smith shows CNN an airplane “black box.” It’s not black, but bright orange.
When an aircraft crashes, this equipment is what investigators are looking for. It’ll give them an insight into what went wrong.
Once a part is ready to be shipped back to the aircraft, it’s sent off by courier with a tracking device so everyone can see where it is.
Overall, it’s a very manual process. Smith says that while there could be advantages of the warehouse operating in a manner more akin to online shopping juggernaut Amazon, the nature of the goods AJW is processing would make that tricky.
“It’s the quality, it’s the paperwork, the process of inspecting the parcel,” says Smith.
“And also, it’s about the money you’re dealing with. You can’t just get a part in here and put it on a shelf without looking at it.”
Still, in the three decades he’s been with the company, Smith’s still seen technology transform AJW’s process. Plus, he notes, the world of aviation is constantly changing and growing.
Whiteside echos this sentiment. Back in the day, he says, air crew would have to manually check that all items were on board, in the right place and functioning correctly. Nowawadays, an RFID scanner allows staff to walk through the aircraft and detect when items such as oxygen masks are due to expire.
“That technology is an enabler to make sure the whole aircraft can be scanned wirelessly to tell you what the shelf life is on your items,” he explains.
As for the aviation industry more generally, Whiteside says it’s on the up. His view — not surprising for someone who pilots his own helicopter — is that even if people might be more environmentally conscious, they’re always going to want to fly.
“The aircraft have become lighter, more fuel efficient. They go further, and so on. And the fact is that people are going to want to get to Peru via air,” he says.